2 min read
WRC & FEA: Piping & Nozzle Stress Validation
Paulin Research Group
Dec 15, 2022 8:48:28 AM
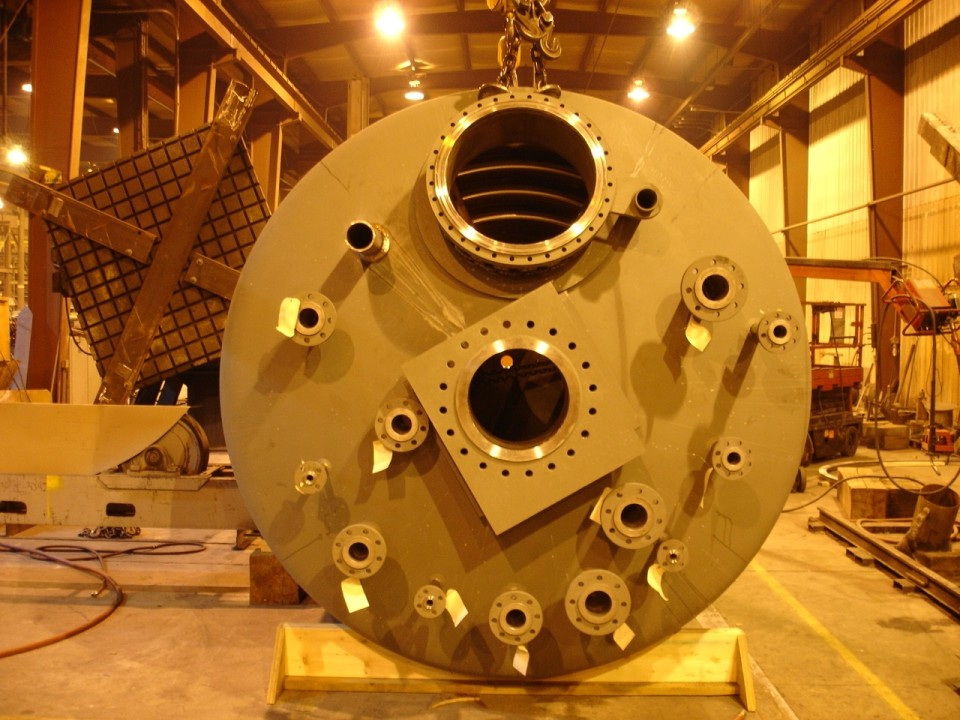
As a pressure vessel designer, you know the importance of designing your equipment in compliance with ASME Section VIII, Div. 2, PD5500 or EN13445 codes. But validating stresses on nozzles can be particularly challenging, even for the most experienced engineers.
And, manually filing compliance reports can be arduous and time-consuming. Without the proper design procedures, you could spend countless hours revising and re-validating your pressure vessel.
How WRC Bulletins validate Nozzle Designs
To help fabricators design proper pressure vessels easily, the Welding Research Council (WRC) develops procedures and equations in the form of a “bulletin,” which guides engineers on addressing a limited scope of geometries.
For example, WRC 107 was developed for extrapolating stresses on nozzles and analyzing rectangular-loaded surfaces on a cylinder. WRC 297 furthers WRC 107 by calculating two normally intersecting cylindrical shells.
As such, for pressure vessel designs, WRC 107 and WRC 297 (and WRC 537) represent one of the simplest and most convenient ways to design a safe and compliant pressure vessel.
These bulletins, however, are not a fix-all solution. As mentioned above, they only apply to a limited scope of geometries, which means they can only account for a subset of geometries. Additionally, WRC bulletins rely on inferred data, meaning that even if your calculation is correct, there may be a blind spot in compliance. This is especially true for geometries outside of the scope of WRC. At this point, you’ll have to find another way to validate designs without having to compromise security to unknown variables.
Finite Element Analysis for WRC 107/537 & 297
For more complicated designs – for example, thin-shelled vessels or multi-nozzle heads – you’ll need an additional form of stress validation to ensure safe and compliant pressure vessel designs.
This is where finite element analysis (FEA) comes in. With FEA, there are no blind spots in your designs as all surfaces, bends and pressures are accounted for. FEA is the only form of validation that adequately predicts and accounts for all the factors that go into pressure vessel design.
But, for many, using FEA can be intimidating. How can you design and model your pressure vessel using FEA and feel more comfortable quickly, with confidence, that you used the method correctly?
FE107: A WRC Piping and Nozzle Stress Calculator with FEA
At Paulin Research Group, we saw the ease of use of WRC 107/537 and WRC 297 but wanted to take the calculations further to overcome their inherent limitations. It’s why we created FE107 – an easy-to-use WRC calculator with built-in FEA capabilities.
Here’s how it works: Simply input your designs into the calculator, click and FE107 will validate the WRC calculation against FEA models.
It's that simple. Design By Analysis compliance for pressure equipment has never been easier. And, the best part? You can easily export your designs to a submittal-ready ASME compliance report.
What's more, the FEA functionality our products provide can reveal blind spots left undetected by a mere WRC calculation.
FE107 is part of both the NozzlePRO and FEPipe design suites. If you’re looking for a better and safer WRC calculator, look no further than FE107. Request a consult today and see how our FEA insights can help you design a safe and compliant pressure vessel faster than ever.