PRG Meshing Solutions
By Product
Tell The Reader More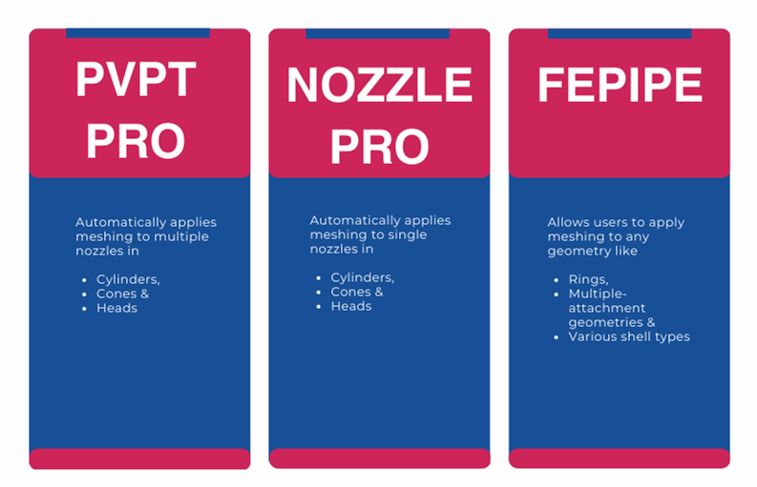
Automatic Meshes for FEA, Multi-Nozzle Geometries
PVPTPro expedites the processing of piping and pressure vessel designs by automatically generating compliant meshes for FEA models containing multiple nozzles. PVPTPro can be thought of as the NozzlePRO for multiple nozzles, and much like NozzlePRO, PVPTPro provides a solution-ready mesh requiring only the dimensional properties, materials and loads from the user.
PVPTPro goes through considerable parametric re-meshing to provide uniform, regular meshes within (RT)0.5 areas of the nozzle penetration lines while using progressively larger element meshes outside the nozzle areas. This can be particularly useful for long cylinders where small meshes over the entire length of the cylinder is unnecessary since this is often provided by general purpose modelers.
Basically, PVPTPro provides a number of mesh support to engineers, including:
1. Getting the first mesh right and requiring little effort from the engineer for mesh adjustment,
2. Providing rectangular element localization between any two or more close nozzles regardless of their orientation, which results in consistent controlling stress calculations and rapid convergence of results,
3. Allowing up to four branch connections or nozzles,
4. Containing rapid ASME/EN code stress reports and animated plots for all combinations of loadings and
5. Providing nonlinear and elastic plastic options with Multi-core Super Node solvers (MCSN) developed by PRG engineers.
Read the latest blog on how this works here
PVPTPro Mesh Density and Convergence Validation
Advanced Meshing for Complicated or Irregular-Sized Geometries
In NozzlePRO, users have a larger set of options to adjust meshing for more complicated components and irregularly sized geometries, which may include some structural supports, saddles, pipe shoes and laterals.
In NozzlePRO, the user has more control over the use of structured and unstructured mesh for the model. read our latest blog about that here
But like PVPTPro, the software makes every attempt to automatically generate a compliant mesh using default parameters. As a result, users can build a wide range of geometries without having to spend extra time on validation and verification.
NozzlePRO also features the automatic solution convergence option during runs, which analyzes the user's model multiple times with different mesh densities to qualify the mesh density necessary and verify that no singularities exist in the model. Once the series of runs is complete, NozzlePRO displays a report to show the mesh convergence.
NozzlePRO Meshing Options and Convergence Reports
Tell The Reader Mor
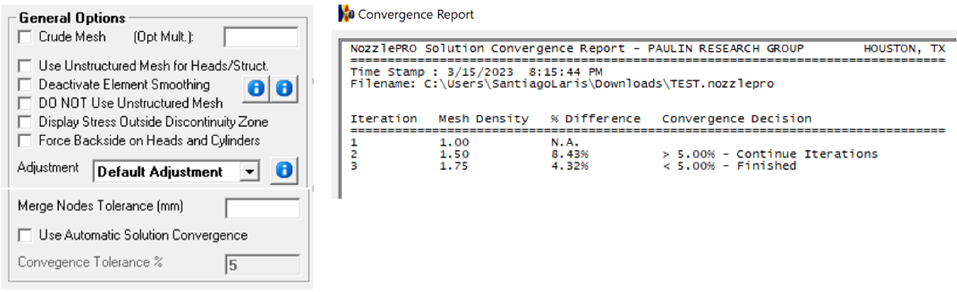
One-Stop-Shop for Advanced FEA
All of the hidden meshing parameters and underlying controls that are not accessible in PVPTPro or NozzlePRO can be accessed in FEPipe.
FEPipe is a one-stop-shop containing a full library of templates for geometries that are available in every other FEA program offered by PRG, but complex models can require significantly more time to build and validate through this interface.
Advanced Meshing Control in FEPipe
Many more options to control the overall meshing exists in FEPipe, which can make complex geometries with multiple attachments arduous to mesh. A wide range of pressure vessel and piping geometries are possible among the available templates, and with proper training and use of FEPipe, users can generate complex models with control over the meshing. For models with multiple attachments, users must pay special attention to various details like:
- Specifying rings and angles for the parent geometry to define the circumferential and longitudinal breakdown of the mesh.
- Controlling the number of elements in nozzle reinforcement welds sections to obtain the proper stresses in these regions.
- Controlling the meshing of plates in structural supports to ensure the edges between plates have merged nodes and are connected properly.
- Surface improvement options and element smoothing options that can fix sharp corners in mesh layout and resolve poorly shaped elements.
- Adding plate geometries of arbitrary shapes and layers either independently or attached to any shell.
- Controlling all analysis options, from which a parent model can be read and connected to others for analysis.
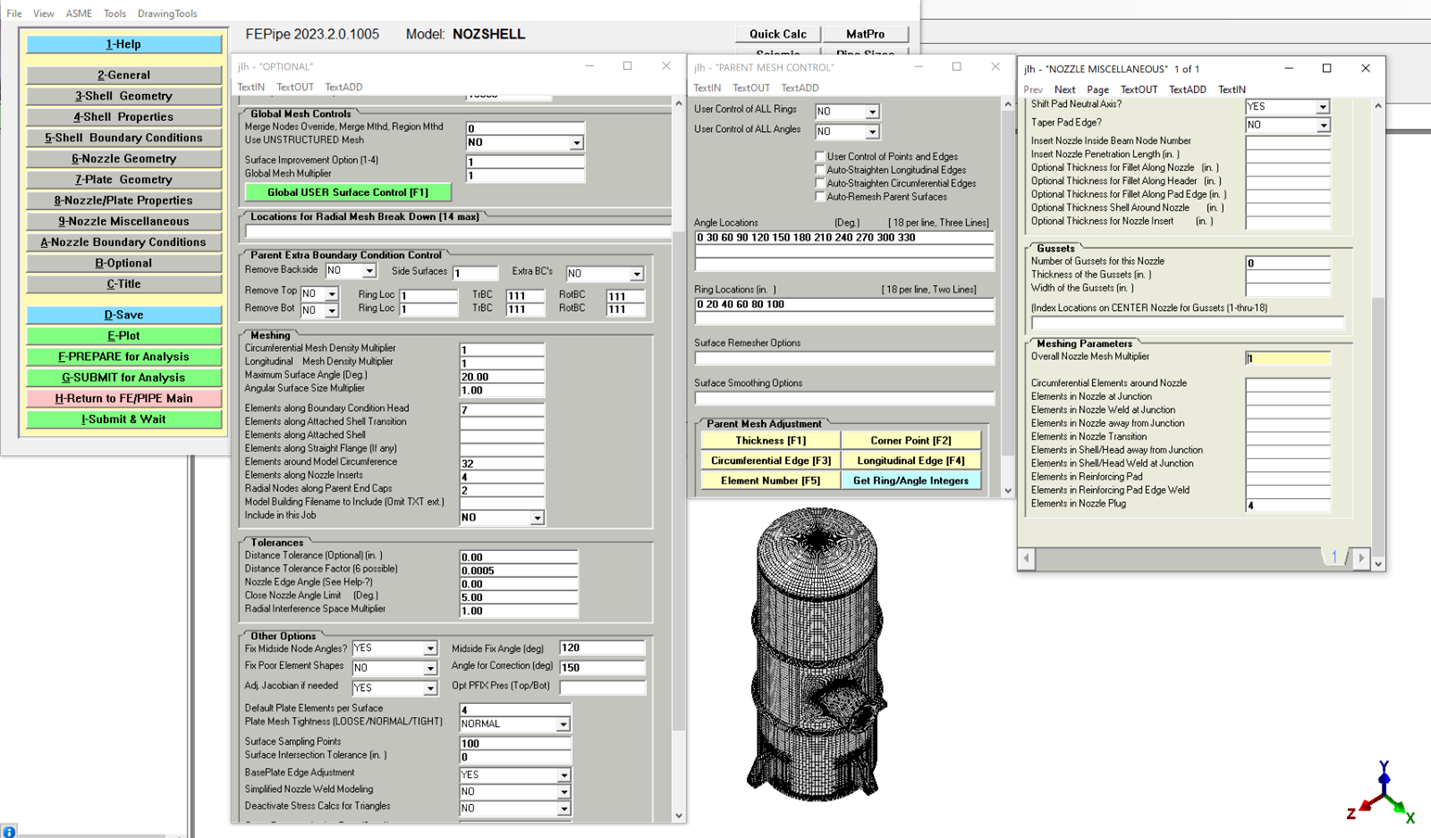