4 min read
PVPTPro: FEA Pressure Vessel Nozzle Design Calculator
Paulin Research Group
Dec 15, 2022 8:49:47 AM
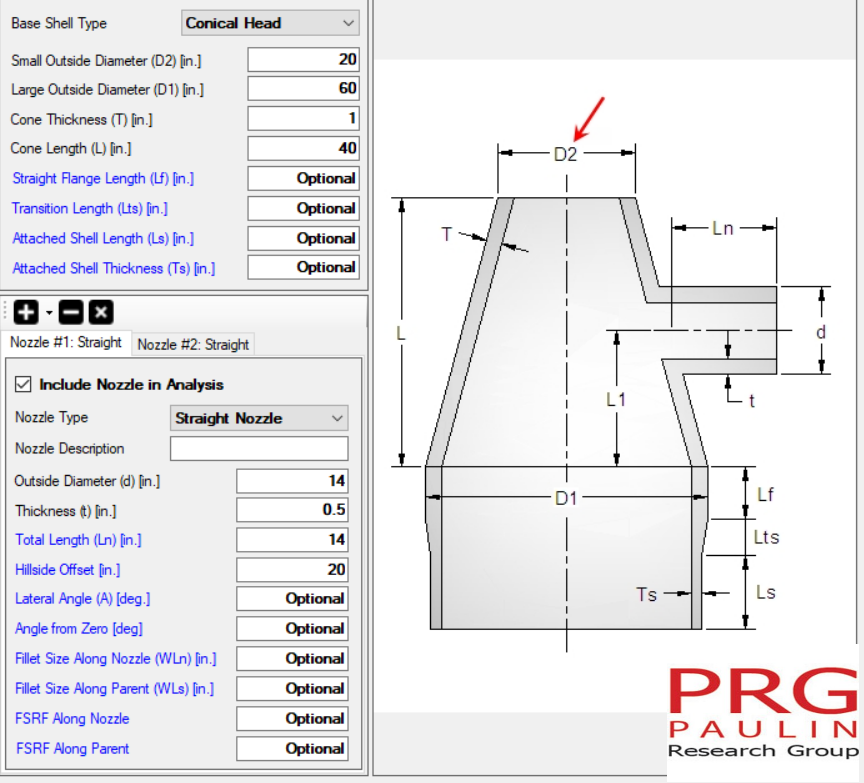
As a pressure vessel designer or engineer, one of the most challenging areas when it comes to compliance is validating the design of your nozzles. While simple forms of validation such as WRC calculations work well for more of your basic designs, they ultimately fail to account for all the factors that go into multi-nozzle designs on more complicated pressure vessel heads.
In these cases, a Design By Analysis (DBA) approach is better for determining proper pressure vessel and pipe stress calculations, stress categories and allowable stresses. But determining this with limited guidance from the codebook or with software that doesn't account for complicated models can take arduous time and money. What if you could design models that have the proper ASME Section VIII, Div. 2, Part 5 nozzle stress calculations? Certain software today not only make it possible, but easy.
PVPTPro: Pressure Vessel Nozzle Load Calculator for ASME
PVPTPro is the latest program released by Paulin Research Group, designed to provide the most efficient and accurate DBA calculation software for pressure equipment design.
PVPTPro allows users to design ASME code-compliant models with multiple nozzles. It uses an FEA approach with 8-noded shell elements to thoroughly solve code concerns.
You can perform FEA on a model with multiple nozzles to produce the most accurate stress results for a vessel, which alternatively outperforms other methods like WRC 107, WRC 297, WRC 537, or STP-PT-074.
PVPTPro bridges the gap between NozzlePro and FEPipe because it allows users to quickly add multiple nozzles on pressure vessel and piping components while also allowing you to easily perform FEA on more complicated models with expanded geometric permutations by using the templates provided in the software, much like NozzlePRO and FEPipe.
Additionally, this new module accounts for hemispherical heads with up to two unreinforced or straight nozzles that can be modeled simultaneously so that the interaction of the stiffness and stresses can be easily analyzed. You can model clustered nozzle designs on a variety of shells.
Ensure Safe & Compliant Conical Head Pressure Vessel Designs with PVPTPro
With today's standards, it's critical that pipe stress calculations on nozzles are accurate, especially with nozzles on conical heads. When these calculations are off, the damages could be catastrophic, both financially and compliance-wise. The only way to adequately calculate stress on these types of designs is by using FEA, which allows you to model one or multiple nozzles simultaneously in close proximity to each other. Without FEA, you risk blind spots in your stress analysis.
But, FEA can be difficult to implement without already having explicit training or knowledge, which can take years. With PVPTPro, performing FEA is simple and can act as an alternative validation method in getting an accurate pipe stress calculation.
PVPTPro also includes a cylinder parent/host option so that both single nozzles and nozzle clusters can be modeled for safety in a vessel shell for either horizontal or vertical vessels. This functionality lets you determine the correct stiffness interaction between two nozzles in a vessel or at the shell wall.
When the codebook or DBA methods have limitations within their processes, PVPTPro’s modular approach helps designers and engineers achieve the proper stress calculations every time.
Design Multiple Nozzle Pressure Vessel Heads At The Same Time
Most pressure equipment design software solutions don’t have the capability for engineers to model multiple nozzles simultaneously while accounting for pressure and external loadings at the same time. Solutions like these can slow designers down or complicate their analysis with models that have multiple reinforced or unreinforced nozzles.
But with PVPTPro – since it is an extension of PRG’s finite element analysis software – you can simultaneously account for the stiffness between two or more nozzles, resulting in properly calculated, safer designs.
Additionally, multiple pad-reinforced nozzles, heavy barrel, or unreinforced nozzles can be modeled simultaneously while using PVPTPro. This is crucial as pad-reinforced nozzles protect the shell around the nozzle by providing additional thickness. PVPT allows you to account for the interaction between the pad and nozzle, as well as the interaction of the pad to the shell weld, so that accurate stress calculations are continually provided.
And what's more, nozzles can be located anywhere on the shell, like the center of the head, offset from the center, and even tilted.
Nozzle Analysis, Stress Calculations, & More
With PVPTPro and in FE107, determining the stress categorization and generating code compliance reports are as easy as inputting variables and clicking a button. PVPTPro expedites a process that generally takes much effort and time. What's more, if the model is code-compliant, model results are instantly displayed.
You can also plot code stresses on your model.
ASME Section VIII, Div. 2 Validation Reports Made Easy
Because all pressure vessels have nozzles, all nozzles are subject to some sort of external load. Often, this can be overlooked during initial design, and what’s more, the supported methods that have been published to aid in the design can be limited in their scope.
For example, most published methods today provide narrow guidance on certain loadings, only provide insights on specific host types and sizes (head vs cylinder, cylinder vs reducer, etc.) or even fail to account for a radial offset, tilt, or repad.
Paulin Research Group’s standalone FEA solution, NozzlePRO, helps to account for some of these loopholes. NozzlePRO supports and analyzes multiple loading options and a variety of host types and sizes but is designed to support one nozzle or attachment at a time.
While ASME Section VIII Div 1 and 2 provide methods for evaluating multiple nozzles under pressure loading, it fails to provide explicit guidance on multiple nozzles under external loads. PVPTPro solves this problem.
By design, PVPTPro is not limited by certain pressures or a single nozzle. Instead, it allows users to quickly design and perform FEA on more complicated models with expanded geometric permutations without having to pull in various design tools or applications.
The Importance of a Modular Approach in Design Software
If you’re a designer or engineer who wants to take on the challenge of more complicated pressure vessel designs, but don’t want to worry about complex ASME compliance reporting or be limited by inadequate stress analysis calculations like WRC bulletins or limited guidelines in the codebook, consider Paulin Research Group's FEA software.
If you’re ready to make safe and compliant pressure vessel designs faster than ever and be done worrying about unknown stress points, request a consultation today.